Graphic material
At the beginning of everything there is an artist, graphic artist, painter, sculptor, ... - simply a medal maker, whose task is to create a proposal of a mintage.
- The medal maker will process a plastic model of a future coin magnified several times on the basis of a sketch or other graphic material (1). He or she uses a nylon plate on which he or she models a clay relief (2). It is then poured into the plaster (3) and formed to the desired final form. Some medal makers then do not work with clay, but engrave the plaster.
- Modern technologies enable to avoid manual modeling and process the relief model in digital form (4), but the honest work of medal makers cannot be replaced. Modern coinage uses the best of both worlds, and handicrafts are often combined with digital ones.
- A separate production chapter is the creation of replicas of historical coins. First of all, the original period coin is imprinted in a special silicone rubber. The rubber imprint is soaked in toluene, which swells by up to 25%. Gypsum is then poured into the thus formed flexible mold, which after hardening represents a slightly enlarged image of the original coin. This gypsum casting is reprinted into the rubber and the whole enlargement process is repeated as many times as necessary to create a gypsum model of the required size (5).
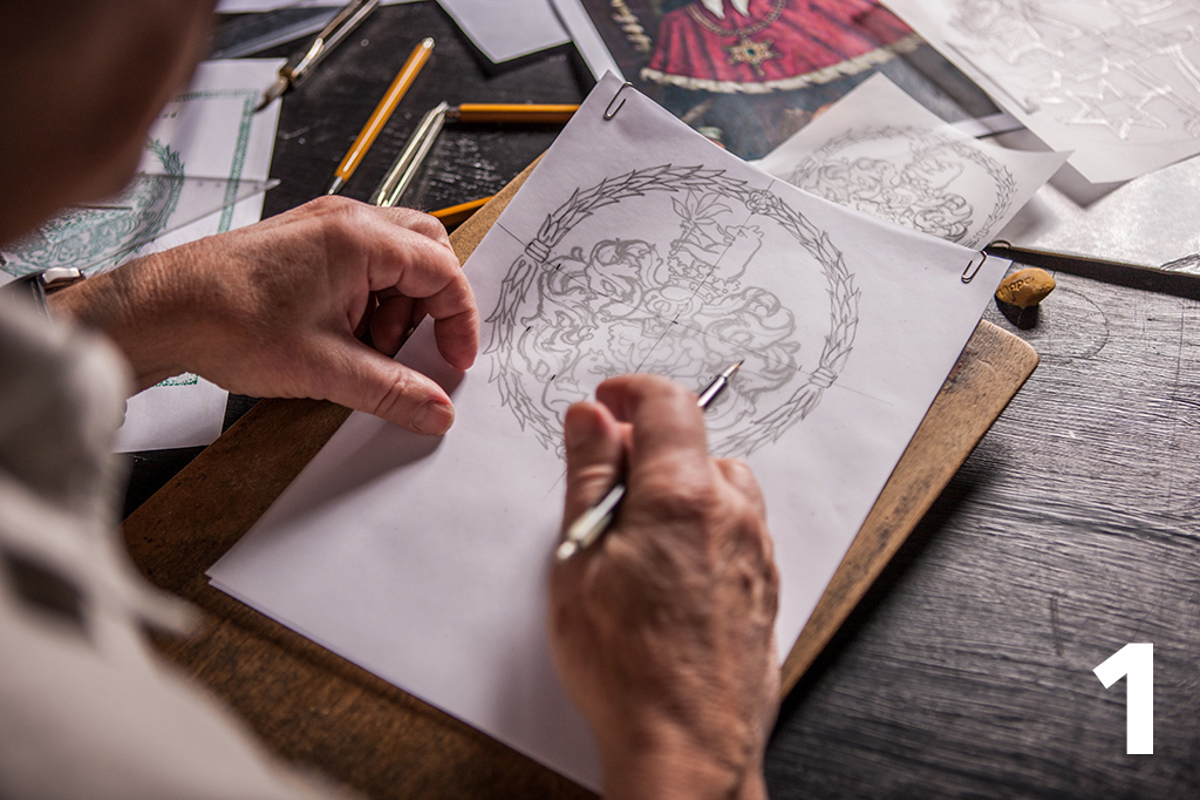
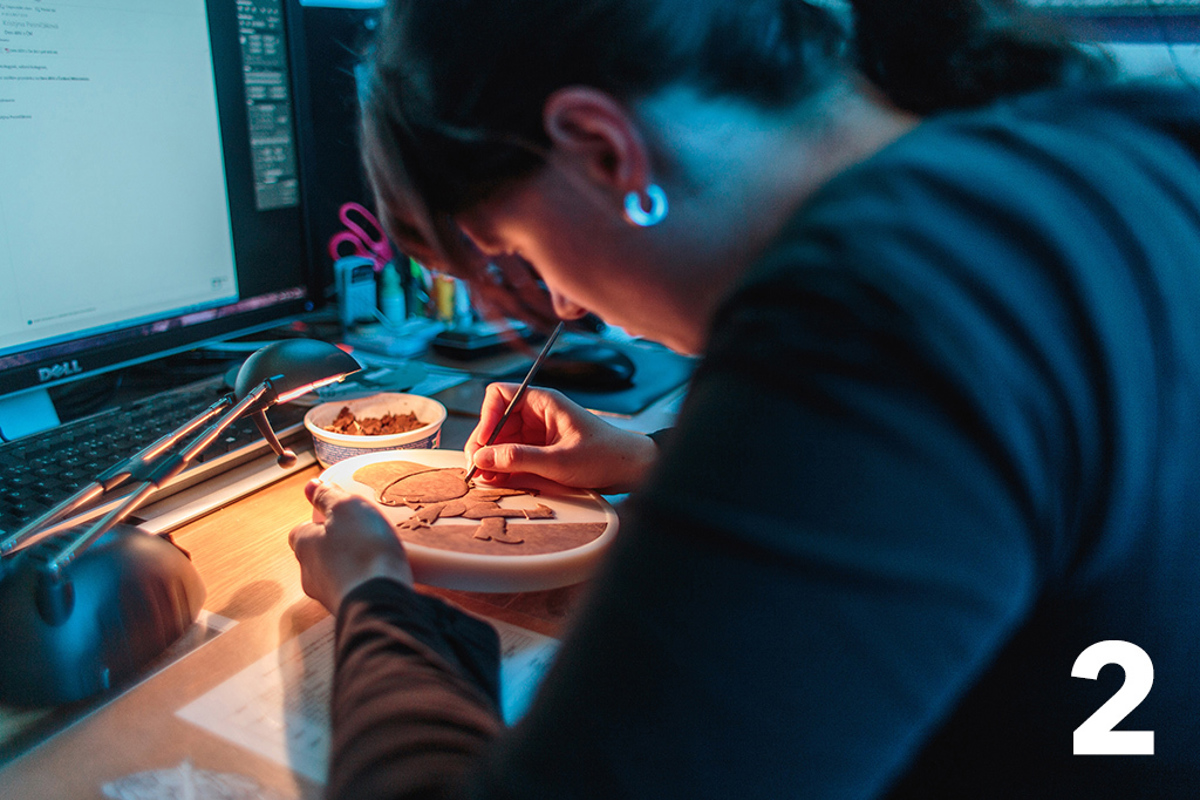
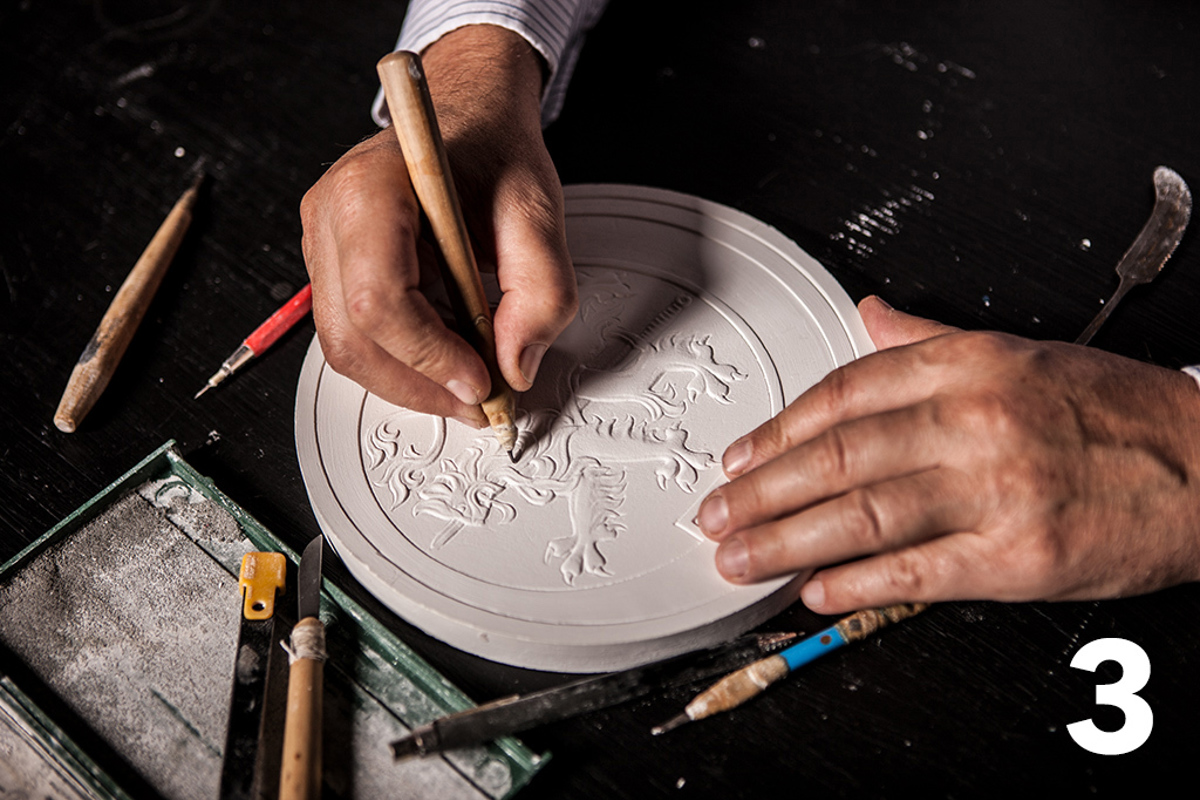
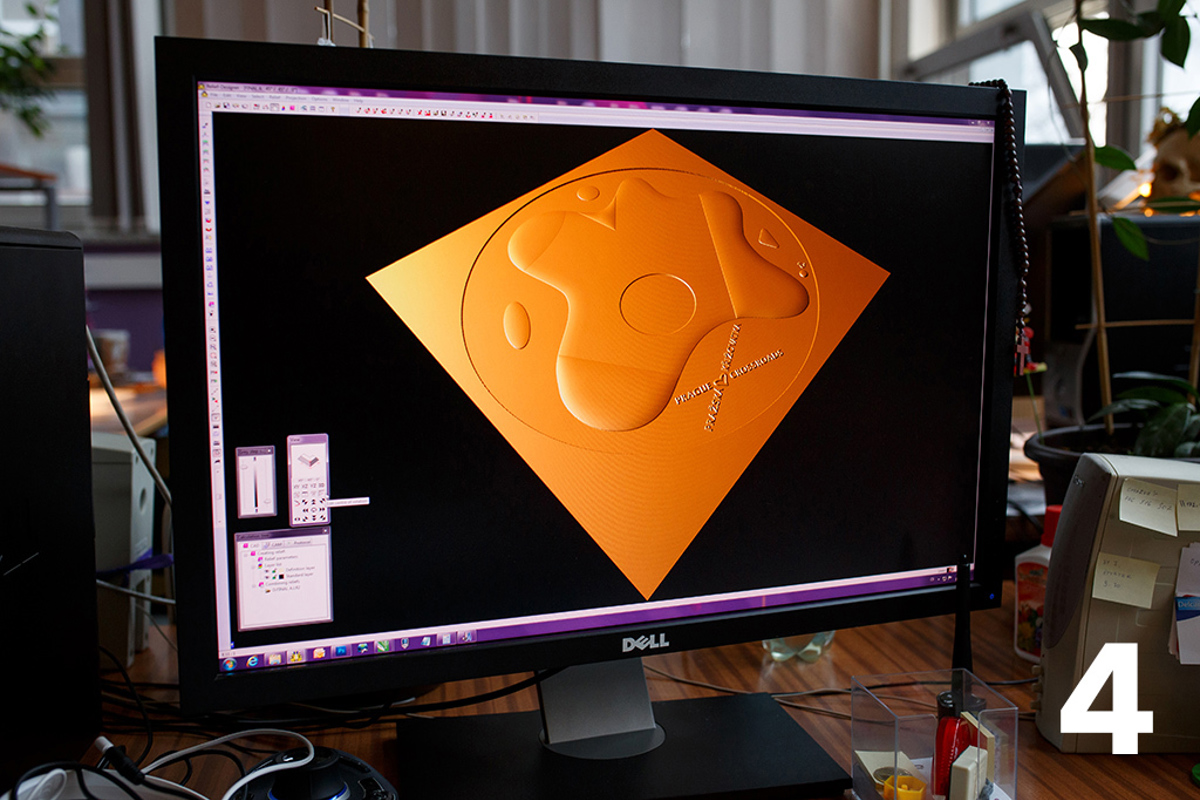
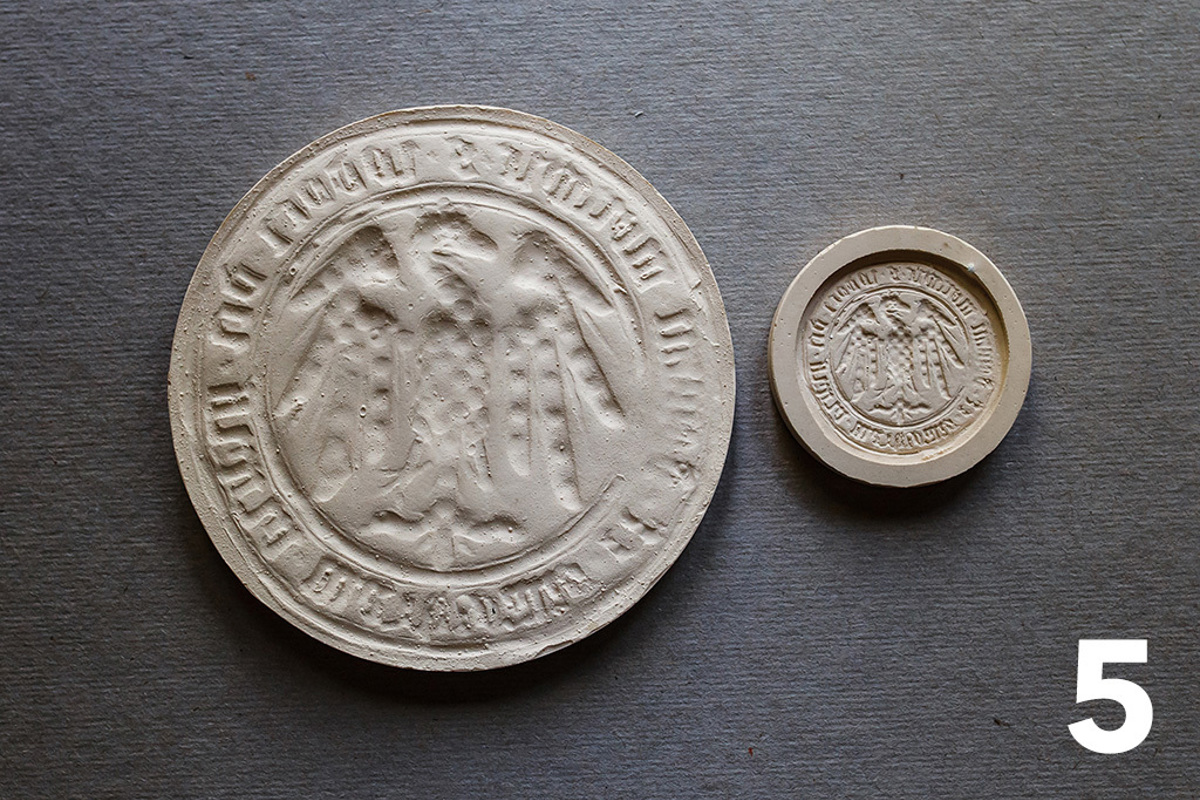
1 – drawing template / 2 – clay model / 3 – plaster model / 4 – digital relief / 5 – enlarged cast
Reduction
The plaster model must then be reduced and transformed into a metallic form.
- A laser (6) is used for this purpose. The model is scanned without contact and converted into a digital form, which is then further modified. The final data is engraved by a computer-controlled machine tool into a steel cylinder (7).
- An alternative method is to use a traditional, purely mechanical reduction machine. The principle is the same, but there is no digital technology - the relief of the model is transferred directly to the steel cylinder via gears and a stylus (8). However, this approach first requires the creation of a silicone casting and then a hard resin copy of the original gypsum model, which resists the action of the stylus (9). This mechanical method is used in the production of coins for the Czech National Bank. It is not only more traditional, but also more secure - it does not create digital data that could be stolen and misused.
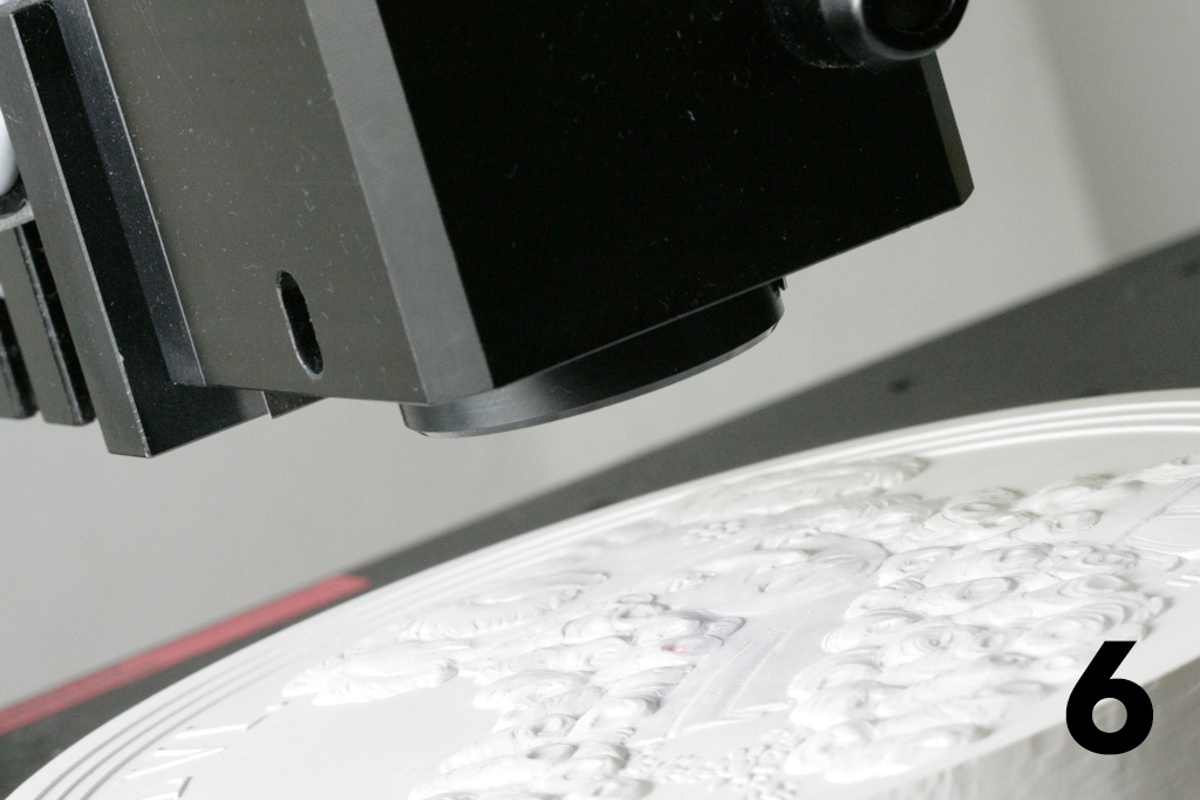
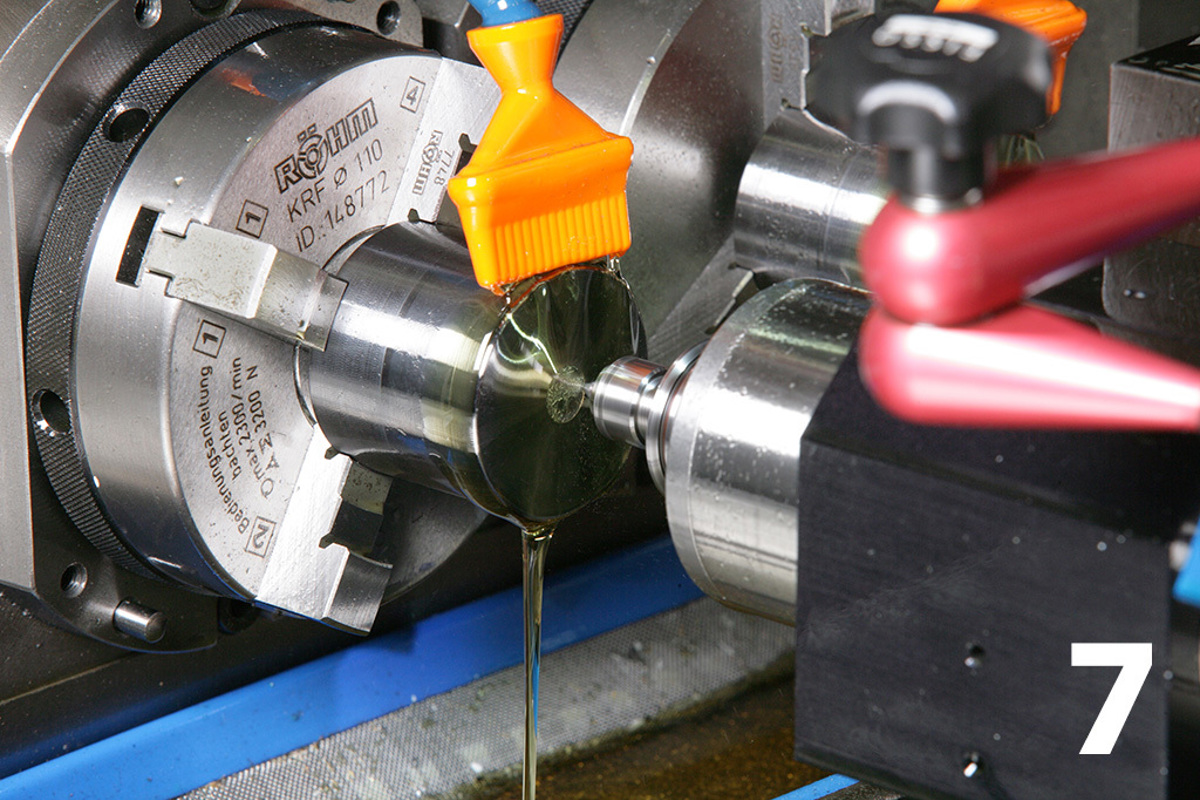
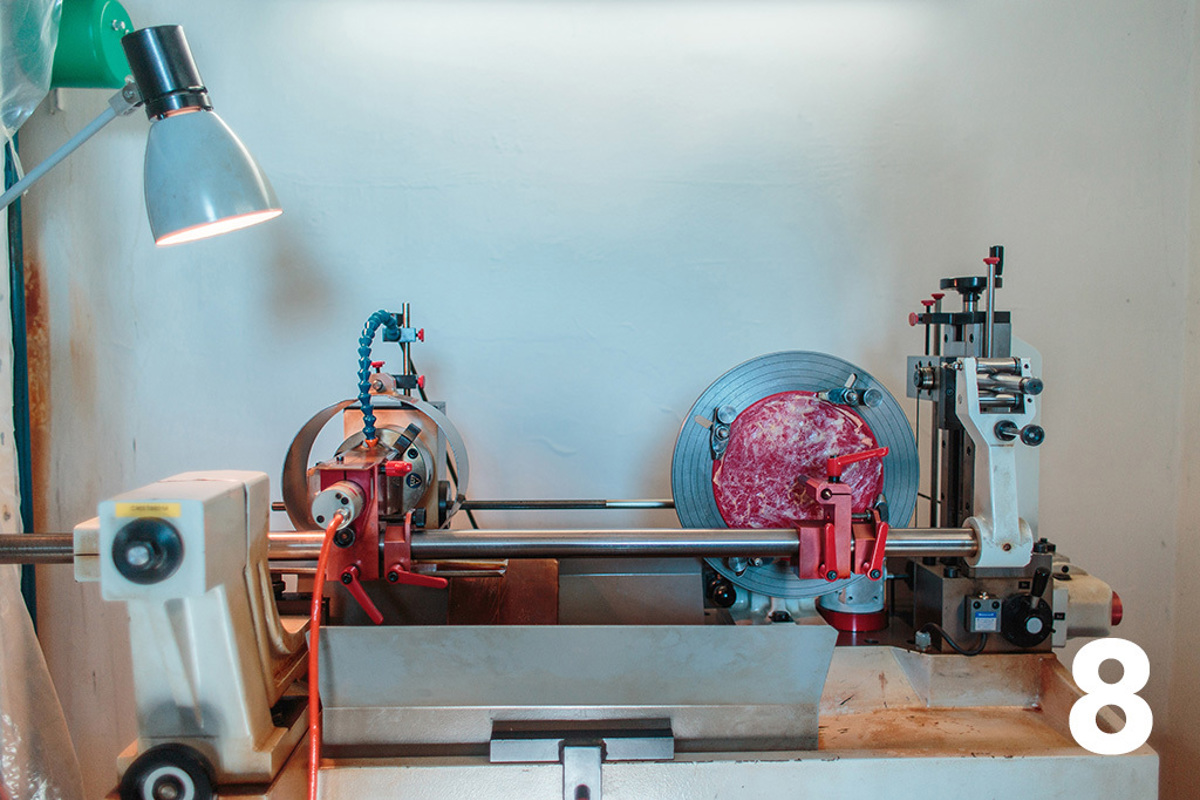
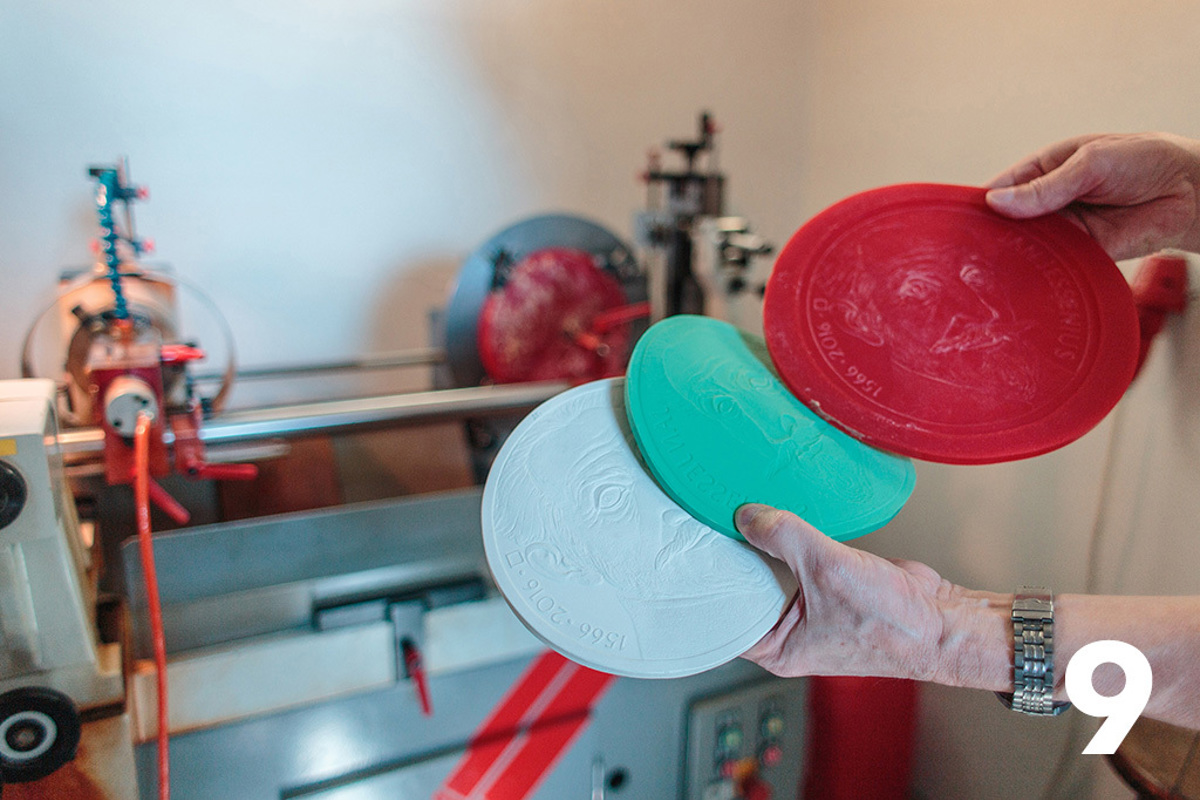
6 – laser scanner / 7 – computer controlled machine tool / 8 – mechanical reduction machine / 9 – resin model
Stamping die
This procedure created the so-called reduction (also called the original) - a reduced positive image of the model, from which a stamping die needs to be produced.
- The reduction is first processed by the engraver who removes the material using spades of various shapes (10). This will eliminate imperfections caused by machine processing and possible mistakes of the medal makers. If the reduction was made by a mechanical reduction machine, much more engraving is required than when using a more accurate laser scanner. The reduction is then cured by turbidity.
- The reduction is imprinted on another steel cylinder, creating a so-called matrix, i.e. die, an inverted image of a future coin. If the engraver has narrowed the relief through positive reduction, he or she can widen it through the negative matrix. Also the matrix is finally cured.
- The imprint of the die into another steel cylinder creates the so-called punch, i.e. die, again a positive image of the future coin, by means of which the final working stamping dies (11) are pressed after hardening, which can be reproduced in this way at any time.
- When the resulting dies are used to mint only a small number of coins, they do not need to be changed, the whole process can be simplified and shortened - because the dies can be produced by reduction, thus avoiding the interphase of matrix and punch. In some cases - for example in the case of kilogram coins - even a gypsum masterpiece is reduced directly to a negative stamp shape.
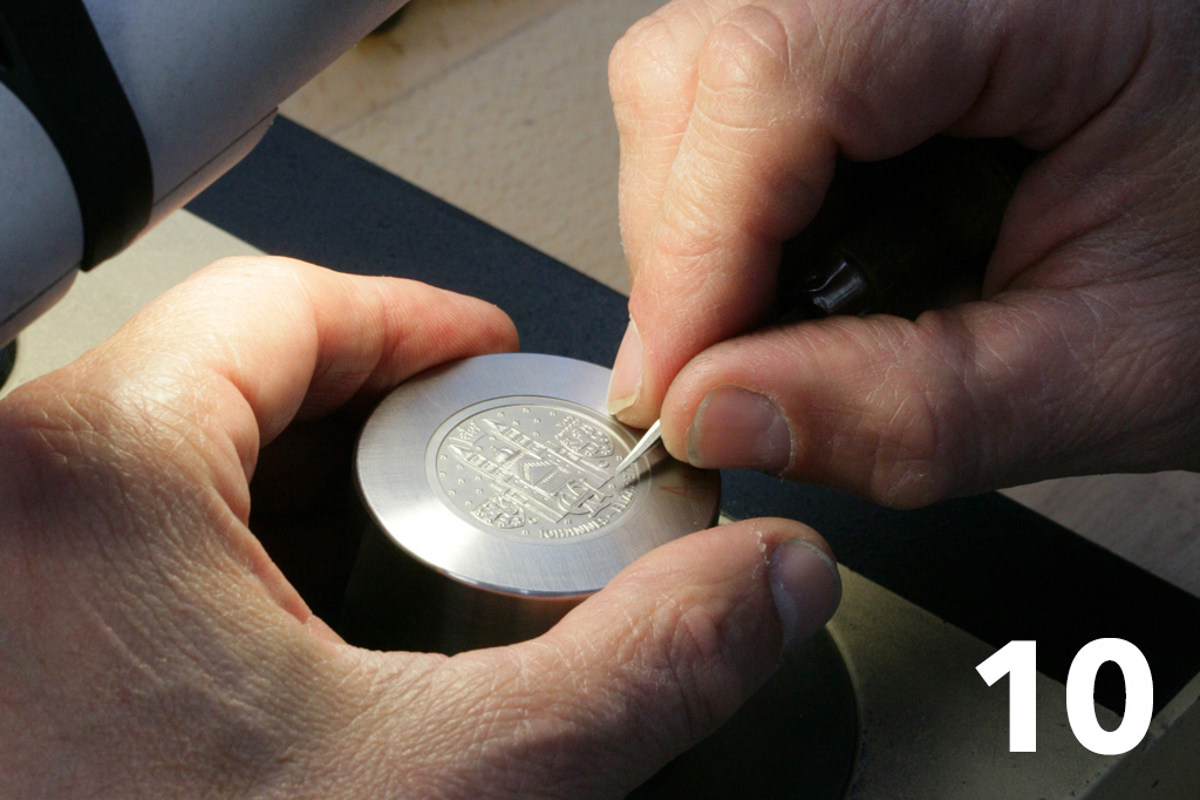
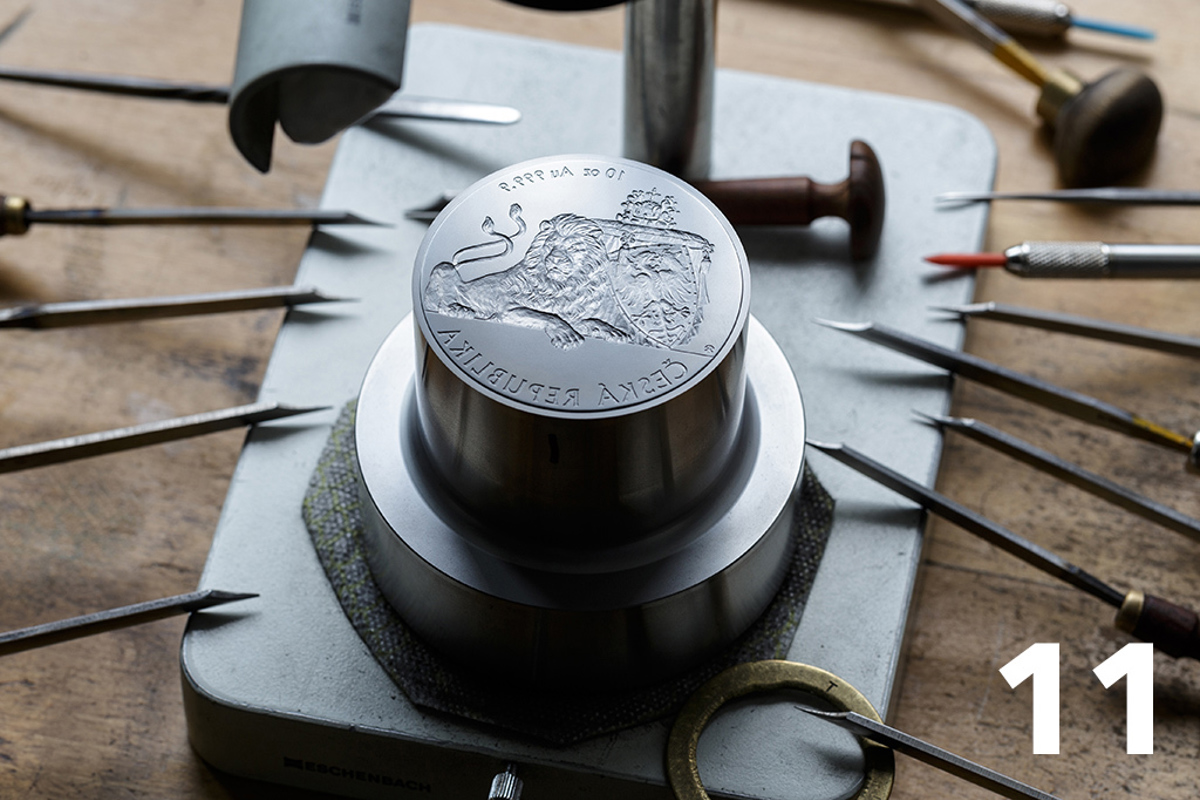
10 – engraving work / 11 – stamping die
Proofing process
Some coins are minted in the so-called quality proof, which is characterized by a mirror-shiny surface and a matte relief. This contrast effect is achieved by a special surface treatment of the stamping dies.
- At the beginning of the proofing process, the surface of the entire die must be polished with special tools and diamond paste (12).
- The surface of the polished die is then covered with a special adhesive tape. On the parts of the relief that are to be matte, the proofer will carefully cut and remove the tape (13) - this procedure must be applied to even the finest details, and so it is performed under a microscope.
- Sand of various roughness is then applied to the hidden die, which makes the exposed parts of the relief matte. Finally, the remaining tape is removed, which has retained selected parts of the relief polished.
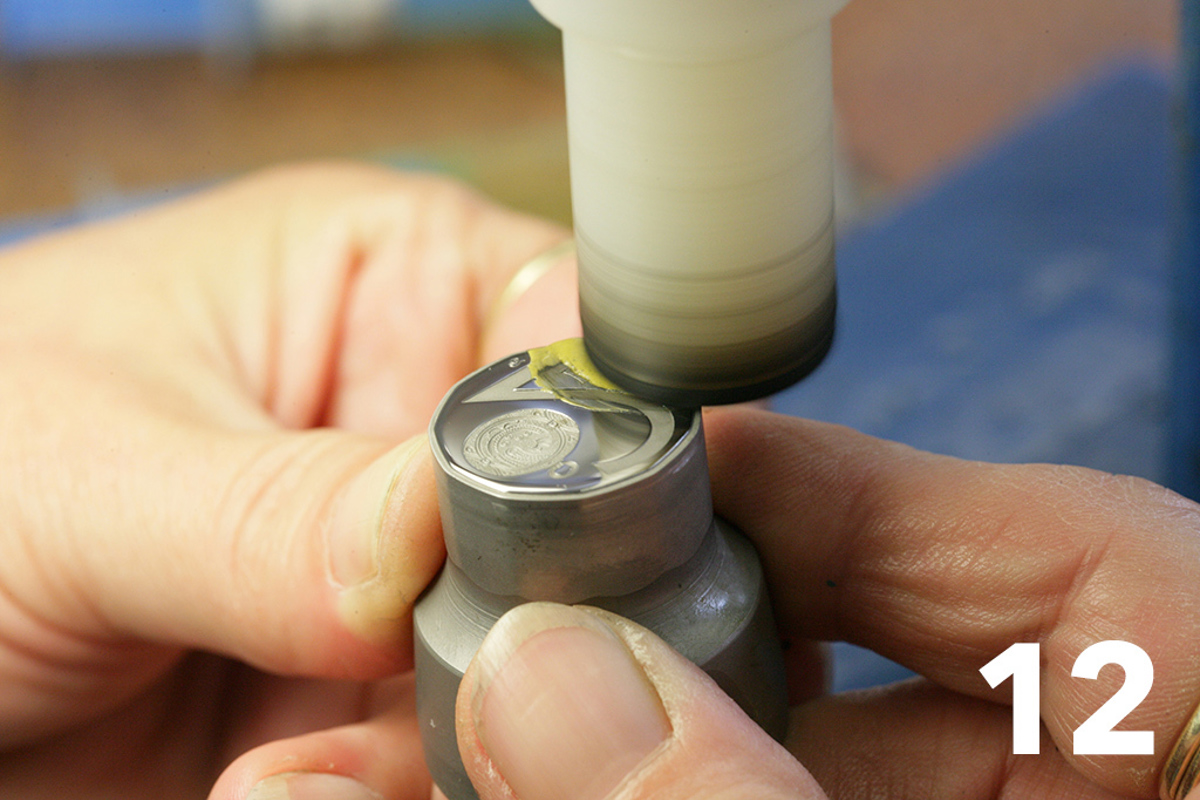
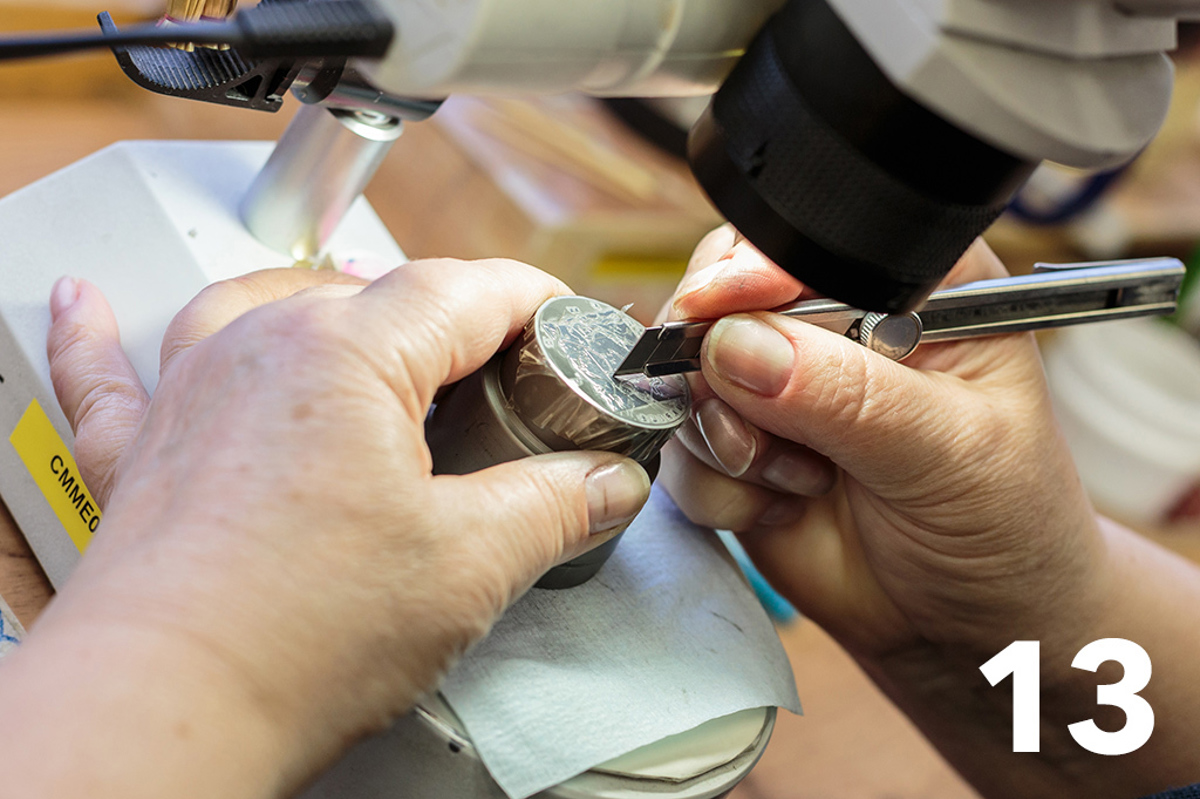
12 – die polishing / 13 – removing the cover tape
Minting
The next step is the minting itself, when the relief of the stamping dies is transferred to the so-called blanks, i.e. semi-finished products of future coins.
- The minting takes place on special presses, into which three tools are clamped - a face stamping die, a reverse stamping die and a pressing ring, which indicates the circumferential shape of the mintage (14).
- Reputable foreign suppliers provide the Czech Mint with blanks (15) whichare carefully inspected. They can be made of base metals and alloys or precious metals. Depending on the type of embossing, they are fed into the press automatically (16), which is the case of circulation coins, or manually (17), in the case of commemorative coins.
- Coin presses can stamp 13 circulation coins per second with a maximum capacity of 500 million pieces per year, using a pressure of up to 150 tons. In the production of kilogram commemorative mintages from platinum, a special hydraulic press must develop a force in excess of 600 tonnes.
- Minted coins are also thoroughly inspected (18). Circulation coins are sealed in plastic bags, which are stored in security containers, on an automatic packaging line. These are then transported by an armored convoy under the supervision of an armed police escort from the Mint in Jablonec nad Nisou to the vaults of the Czech National Bank.
- In addition, each commemorative coin is placed in a plastic capsule to prevent the ingress of air, dust and other undesirable effects. A coin minted in quality proof can be devalued even by a mere human touch - the touched mirror-shiny surface cannot be polished again to its original form.
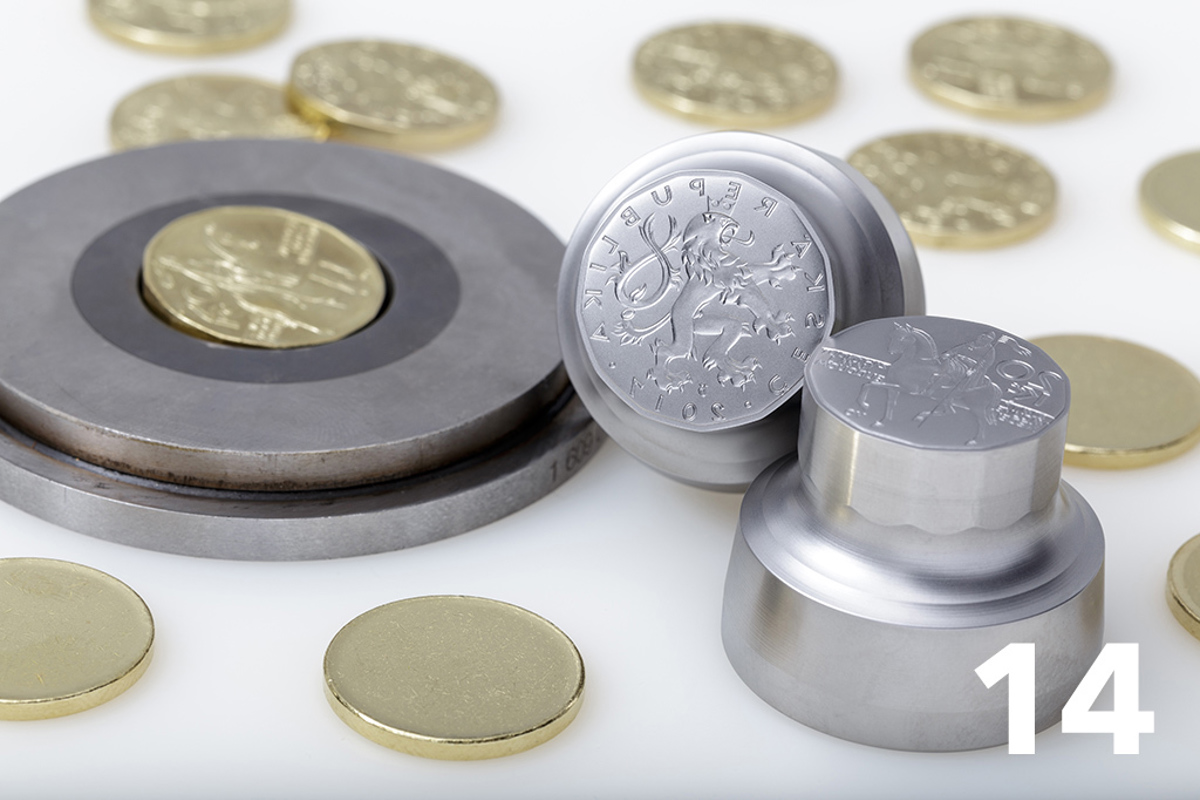
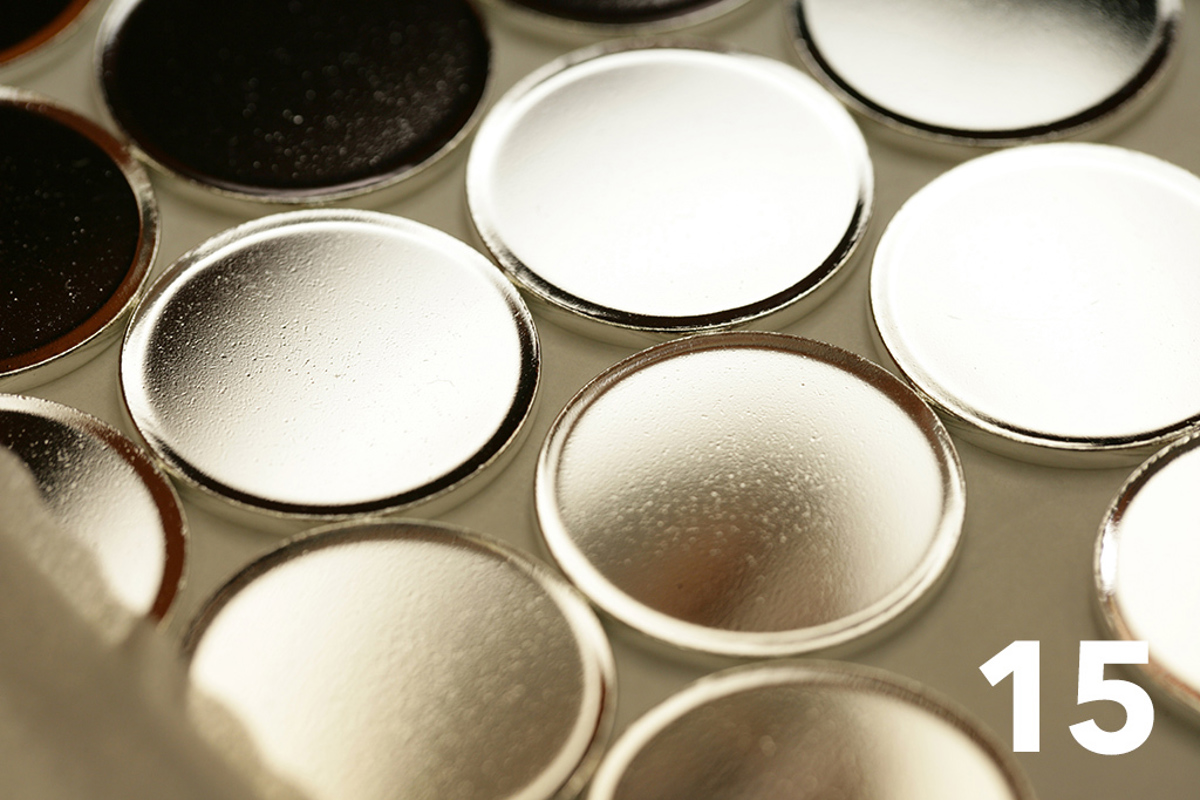

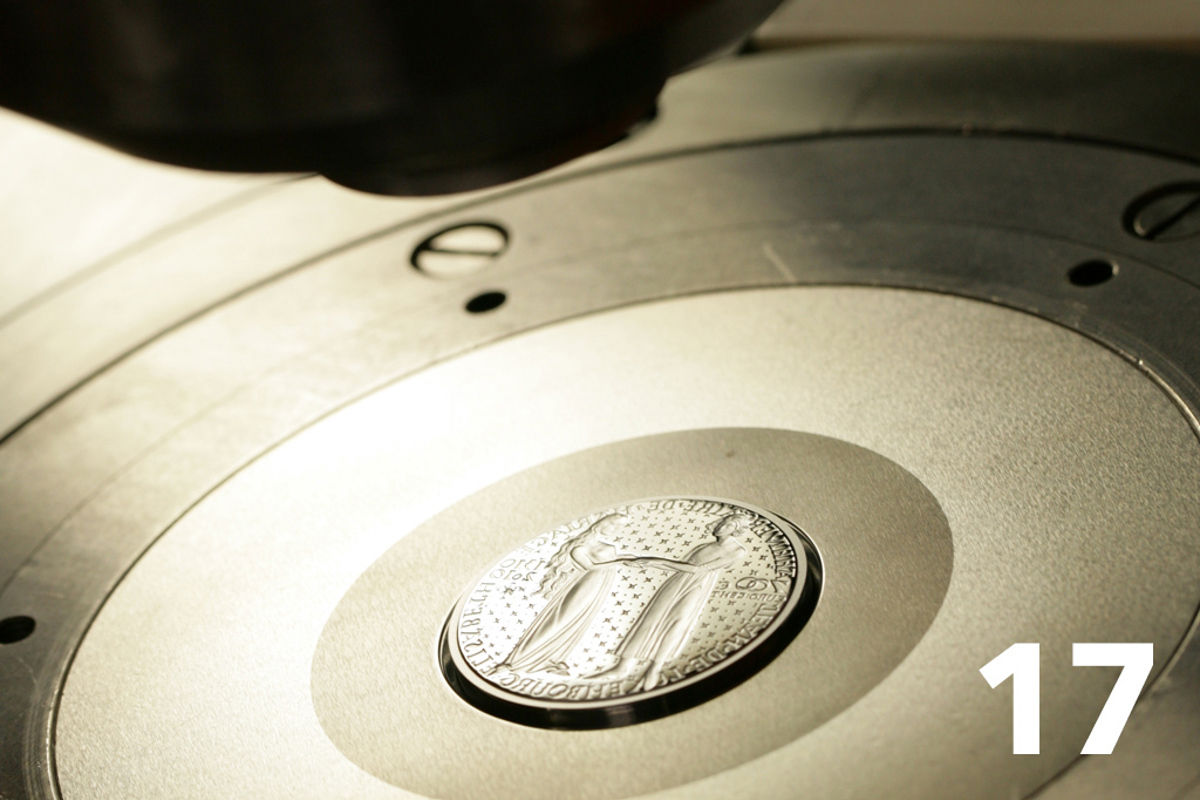
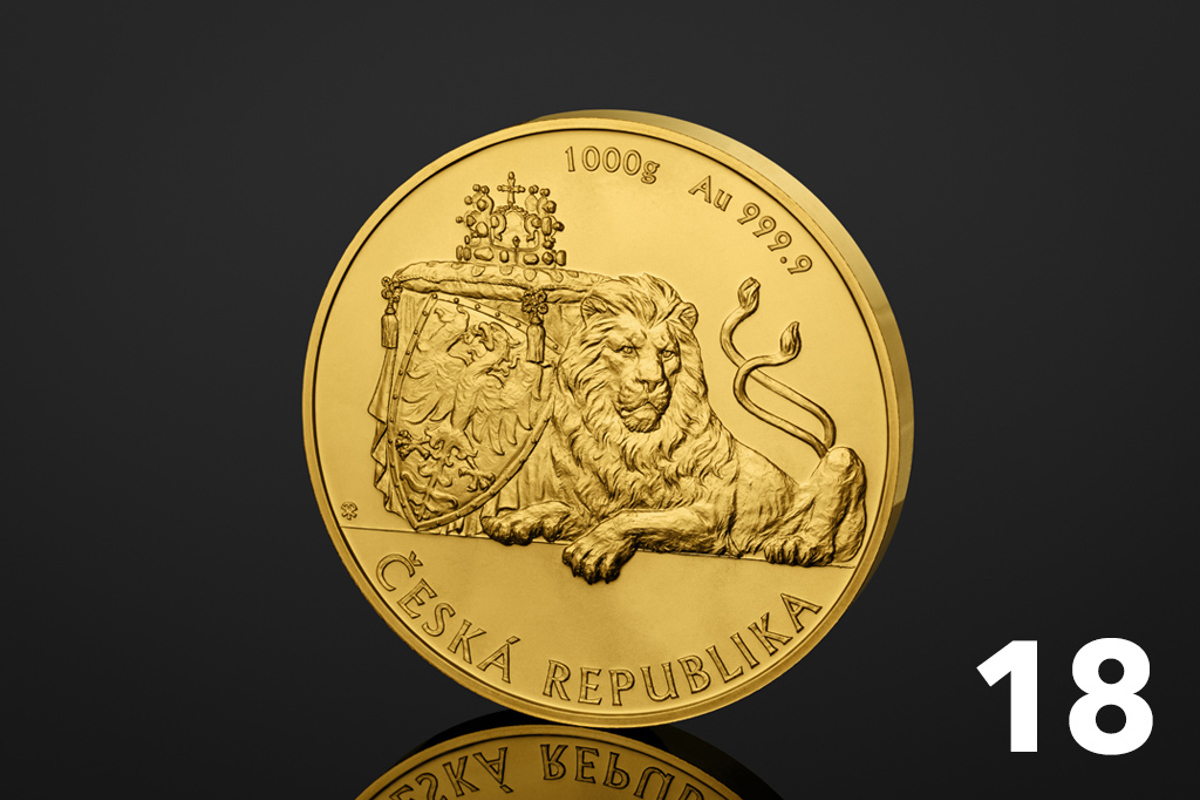
14 – embossing tools / 15 – blanks / 16 – coin press with automatic feeding of blanks / 17 – medal press with manual feeding of blanks / 18 – finished coin
Coin production is a process that is never the same. Depending on the type of final product, additional steps may be added to the entire manufacturing process and some of it may be set aside.